Safety in Ethanol Manufacturing: Key Considerations
- hr30522
- Sep 4, 2024
- 8 min read
Updated: Nov 22, 2024
Ethanol manufacturing plays a pivotal role in the global energy landscape, offering a renewable fuel source and serving as a critical component in various chemical processes. However, the production process involves handling volatile substances, operating high-pressure equipment, and managing hazardous chemicals, which poses significant safety risks. Addressing these risks through effective safety protocols, advanced technologies, and robust safety culture is essential for ensuring a secure and efficient workplace. This guide explores the key considerations for safety in ethanol manufacturing, highlighting essential protocols, advanced safety technologies, and strategies for continuous improvement.
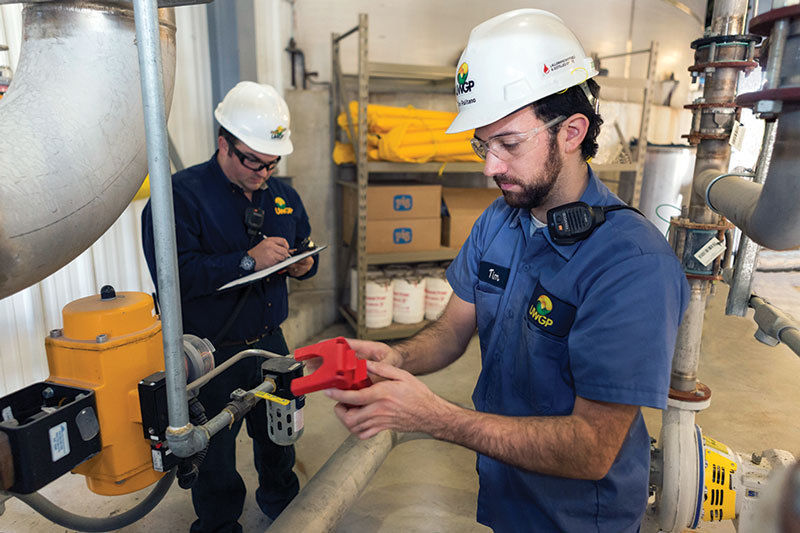
Understanding the Risks in Ethanol Manufacturing
Fire and Explosion Risks
Ignition Sources: Ethanol vapors are highly flammable and can ignite from sources like electrical sparks, open flames, and static electricity. To mitigate these risks, ensure that electrical equipment is properly grounded, use explosion-proof fixtures, and manage static electricity by employing grounding and bonding techniques.
Explosion Risks: Ethanol vapors can form explosive mixtures in confined spaces. Effective ventilation is crucial to prevent vapor accumulation. Implementing regular maintenance checks on ventilation systems and using explosion-proof equipment can significantly reduce the risk of explosions.
Chemical Exposure
Chemical Handling: Proper handling techniques and the use of personal protective equipment (PPE) are essential. Workers should wear appropriate PPE, such as gloves, goggles, and face shields, and chemicals should be stored in well-ventilated, labeled containers. Safety Data Sheets (SDS) should be readily available for reference.
Health Monitoring: Regular health check-ups and monitoring programs are necessary to detect any adverse effects from chemical exposure. Health surveillance helps in early identification and intervention, reducing the risk of long-term health issues.
Equipment Failures
Maintenance and Inspection: Establish a routine maintenance schedule that includes regular inspections of equipment to identify and address issues before they lead to failures. Regularly check for leaks, corrosion, and wear and tear.
Emergency Shutoff Systems: Install automatic shutoff systems that activate in response to abnormal conditions, such as high pressure or temperature, to prevent accidents. Regular testing and maintenance of these systems are crucial to ensure their reliability during emergencies.
Essential Safety Protocols
Compliance with Regulations
OSHA Standards: Compliance with Occupational Safety and Health Administration (OSHA) regulations ensures safe handling of hazardous materials, emergency preparedness, and worker training. OSHA standards provide a framework for managing workplace safety and reducing the risk of accidents.
EPA Regulations: The Environmental Protection Agency (EPA) guidelines for hazardous waste management and emissions control help minimize environmental impact and ensure responsible waste management. Adhering to these regulations is crucial for preventing environmental contamination.
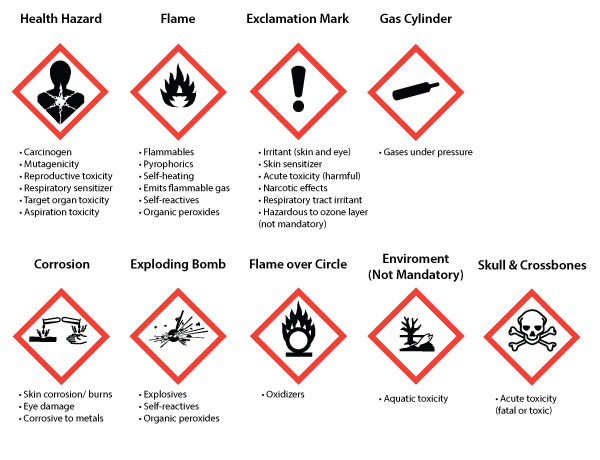
Training Programs
Initial Training: New employees should undergo comprehensive training on the hazards associated with ethanol manufacturing, safe equipment operation, and emergency procedures. Training should include practical scenarios to prepare workers for real-life situations.
Ongoing Training: Regular refresher courses are important for keeping workers updated on new safety measures, technologies, and regulations. Continuous training reinforces safety practices and ensures workers remain vigilant.
Personal Protective Equipment (PPE)
Flame-Resistant Clothing: Workers should wear flame-resistant clothing to protect against fires and high temperatures. These garments are designed to withstand extreme conditions and reduce the risk of burns.
Safety Goggles and Face Shields: Protective eyewear is necessary to prevent injuries from chemical splashes, flying debris, and high-pressure releases. Face shields offer additional protection for the face and neck.
Gloves: Choose gloves based on the chemicals handled and the tasks performed. Chemical-resistant gloves protect against skin contact with hazardous substances.
Ventilation Systems
Local Exhaust Ventilation: Local exhaust systems capture and remove contaminants directly from their source, preventing the buildup of flammable vapors and maintaining a safer working environment.
General Ventilation: Provide continuous fresh air flow to dilute contaminants and maintain overall air quality. Proper ventilation design helps ensure that vapor concentrations remain below explosive levels.
Fire Suppression Systems
Sprinkler Systems: Foam-based sprinkler systems are effective for fighting flammable liquid fires. Sprinklers should be strategically placed in high-risk areas and regularly tested to ensure proper coverage.
Fire Extinguishers: Provide extinguishers suitable for different types of fires, such as Class B extinguishers for flammable liquids. Ensure extinguishers are easily accessible and that workers are trained in their use.
Emergency Response Plans
Evacuation Procedures: Establish clear evacuation procedures, including exit routes and assembly points. Conduct regular drills to ensure workers are familiar with evacuation processes and can respond quickly in emergencies.
Emergency Contacts: Maintain up-to-date contact information for emergency services, such as fire departments and medical facilities. Ensure workers know whom to contact in case of an emergency.
First Aid: Provide first aid kits and train employees in basic first aid procedures. Prompt first aid can manage injuries and provide immediate care until professional medical assistance arrives.
Risk Assessments and Safety Audits
Risk Assessments: Conduct thorough risk assessments to evaluate potential hazards and their impact on operations and workers. Use findings to develop targeted safety measures and procedures.
Safety Audits: Perform regular safety audits to review safety practices, equipment, and protocols. Audits help identify gaps and areas for improvement, ensuring safety measures remain effective and compliant with regulations.
Advanced Technologies for Safety
Incorporating advanced technologies can enhance safety in ethanol manufacturing:
Leak Detection Systems
Sensor Technology: Advanced sensors detect leaks of gases, liquids, and vapors in real-time. These sensors should be installed in critical areas to provide early warnings of potential leaks.
Alarm Systems: Integrate alarm systems with leak detection sensors to alert workers of the presence of leaks. Alarms prompt immediate action to address leaks and prevent accidents.
Gas Detectors
Portable Gas Detectors: Use portable gas detectors for routine checks and localized monitoring. These devices help assess gas levels in specific areas and take corrective actions if necessary.
Fixed Gas Detectors: Install fixed gas detectors in strategic locations for continuous monitoring. Fixed detectors provide real-time data on gas concentrations and trigger alarms if levels exceed safe thresholds.
Pressure Relief Valves
Automatic Relief: Pressure relief valves are designed to open automatically when pressure exceeds a set threshold, preventing dangerous overpressure conditions. Ensure valves are calibrated and maintained regularly.
Regular Testing: Conduct routine testing and maintenance of pressure relief valves to ensure they function correctly and respond appropriately to overpressure situations. Regular checks help prevent equipment failures.
Explosion-Proof Equipment
Explosion-Proof Enclosures: Use explosion-proof enclosures to house equipment in hazardous areas. These enclosures are built to withstand the forces of an explosion and prevent the release of flammable gases.
Certified Equipment: Ensure all equipment used in ethanol manufacturing is certified for use in explosive environments. Certification indicates that the equipment meets safety standards and is suitable for the intended application.
Advanced Monitoring Systems
Data Analytics: Utilize data analytics to analyze trends and detect anomalies in real-time. Analyzing data helps identify potential safety issues and enables timely intervention.
Integration with Safety Systems: Integrate monitoring systems with other safety systems, such as alarms and automatic shutdown systems, to create a comprehensive safety solution. Integration ensures monitoring data is effectively used to enhance safety measures.
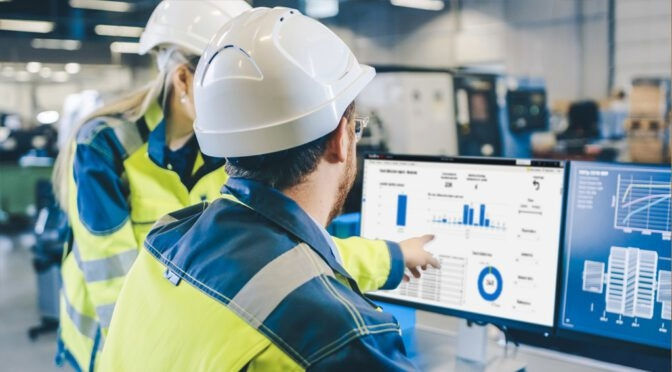
Implementing Safety Measures
Effective implementation of safety measures involves strategic planning, execution, and ongoing evaluation:
Proper Labeling and Storage
Labeling: Clearly label all containers with information about their contents and potential hazards. Proper labeling helps workers identify and handle materials safely, reducing the risk of accidental exposure or misuse.
Storage: Store hazardous materials in appropriate containers and designated areas designed to prevent leaks and spills. Ensure storage areas are well-ventilated and equipped with spill containment measures.
Spill Containment and Clean-Up
Bunding: Create bunds or barriers around storage areas and equipment to contain spills and prevent their spread. Bunds help control the impact of spills and facilitate clean-up efforts.
Spill Kits: Provide spill kits containing absorbent materials, gloves, and disposal bags for cleaning up spills. Ensure spill kits are readily accessible and that workers are trained in their use.
Lockout/Tagout Procedures
Lockout Devices: Use lockout devices to physically lock equipment in the off position, preventing accidental activation while maintenance is performed. Lockout devices should be standardized and readily available.
Tagout Devices: Use tagout devices to provide information about the status of the equipment and warn against reactivation. Tagout devices should include details about the maintenance being performed and the identity of the person responsible.
Safety Signage and Alerts
Visual Signage: Use warning and instructional signs to communicate safety information, such as hazard warnings, emergency procedures, and safety equipment locations. Ensure signage is clear, visible, and updated as needed.
Audible Alerts: Install alarms and sirens to alert workers to dangerous conditions and prompt immediate action. Audible alerts should be loud enough to be heard over normal background noise and should be tested regularly.
Incident Reporting and Investigation
Reporting: Encourage workers to report incidents, near misses, and unsafe conditions promptly. Reporting helps identify potential hazards and address them before they lead to accidents.
Investigation: Conduct thorough investigations of incidents to determine their causes and develop corrective measures. Use investigation findings to improve safety practices and prevent similar incidents in the future.
Safety Culture and Communication
Safety Meetings: Hold regular safety meetings to discuss safety concerns, review incidents, and share best practices. Meetings provide an opportunity for workers to voice concerns and contribute to safety improvements.
Feedback and Recognition: Encourage feedback from workers on safety practices and recognize safe behaviors. Providing positive reinforcement and addressing feedback helps build a culture of safety and encourages ongoing vigilance.
Health Monitoring and Support
Health Surveillance: Implement health surveillance programs to monitor workers for signs of health issues related to chemical exposure or other workplace hazards. Regular health check-ups help identify potential problems early.
Support Programs: Offer support programs, such as counseling and wellness resources, to help workers manage stress and maintain overall health. Supporting workers' well-being contributes to a safer and more productive work environment.

Continuous Improvement
Safety in ethanol manufacturing is an ongoing process requiring continuous improvement:
Regular Inspections and Maintenance:
Inspection Routines: Establish regular inspection routines to check equipment, safety systems, and facilities. Inspections help identify potential issues before they lead to accidents or failures.
Maintenance Schedules: Follow established maintenance schedules for equipment and safety systems. Preventive maintenance helps extend the lifespan of equipment and reduce the likelihood of unexpected failures.
Adapting to New Technologies:
Technology Upgrades: Invest in new technologies and safety equipment to improve safety measures. Upgrading equipment and systems can enhance detection capabilities and provide better protection against hazards.
Innovation and Research: Stay informed about industry innovations and research to incorporate the latest safety practices and technologies. Engaging in research and development helps advance safety standards and practices.
Engaging in Industry Best Practices
Industry Forums: Attend industry forums, conferences, and workshops to learn from experts and peers about the latest safety practices and technologies. Networking with industry professionals provides valuable insights and opportunities for collaboration.
Collaborative Efforts: Share knowledge and experiences with other industry professionals to enhance safety practices. Collaborative efforts can lead to the development of new safety standards and practices that benefit the entire industry.
Evaluating Safety Management Systems
System Reviews: Periodically review safety procedures, policies, and performance metrics to assess their effectiveness. Use feedback from audits, inspections, and incident investigations to make necessary adjustments.
Performance Metrics: Monitor performance metrics, such as incident rates and compliance levels, to evaluate the effectiveness of safety management systems. Analyzing performance data helps identify areas for improvement and ensure safety measures achieve their intended goals.
Encouraging Worker Involvement
Safety Committees: Establish safety committees that include workers from various departments. Committees can address safety concerns, develop new initiatives, and promote a collaborative approach to safety.
Worker Feedback: Encourage workers to provide feedback on safety practices and procedures. Regular feedback sessions and surveys help gather valuable insights and ensure safety measures are effective and relevant.

Conclusion
Ensuring safety in ethanol manufacturing is a complex, multifaceted challenge that requires a comprehensive approach. By implementing essential safety protocols, adopting advanced technologies, and fostering a robust safety culture, ethanol plants can significantly reduce the risk of accidents and create a secure working environment for all employees. Continuous improvement, regular training, and adherence to regulatory standards are critical for maintaining high safety standards and protecting both workers and the environment.
As the ethanol manufacturing industry evolves, staying proactive in safety measures remains essential for resilience and success. Prioritizing safety is not only a regulatory requirement but also a fundamental commitment to the well-being of employees and the sustainability of the industry. Through diligent adherence to safety practices and ongoing evaluation, the ethanol manufacturing sector can build a safer, more secure working environment and ensure long-term success in a dynamic industry landscape.
#Hazard #Compliance #Training #PPE(Personal Protective Equipment) #Ventilation #Explosion-proof #FireSuppression #EmergencyResponse #RiskassessmentSafetyaudits
#Chemicalhandling #Leakdetection #Properlabeling #Safetyprotocols #Monitoringsystems #Spillcontainment #Safetydrills #Firstaid #Hazardousmaterials #Processcontrols #Equipmentmaintenance #Lockout/tagout #Safetysignage #Incidentreporting #Workertraining #StandardOperatingProcedures(SOPs) #Flammablematerials #Temperaturecontrol #Pressurerelief #Gasdetectors #Personalalarms #Firewalls #Bunding #Emergencyshutoff #Safetybarriers #Properstorage #Chemicalspillkits #Ventilationsystems #Safetyculture #Audiblealarms #Visualalerts #Crisismanagement #Environmentalcontrols #Inspectionroutines #Trainingprograms #Safetymanagementsystems #RiskmitigationHealthmonitoring #Incidentinvestigation #Regulatorystandards
Comentarios